my adidas summer!
- saachi poddar
- Sep 24, 2024
- 9 min read
hi there. long time no see. let me catch you up...
This summer I was given the opportunity to intern with adidas as a Product Design Intern for US Sports. I packed my things at the end of spring and drove up with my mom and dad from Eugene, OR to be welcomed to a one-bedroom tiny home just off Greeley Ave. next to the adidas NAMHQ in Portland.
On June 17th, my mom and dad walked me to my first day of work where, unsurprisingly, I accidentally showed up an hour early. After waiting for the time to pass, I coincidentally sat next to three girls who ended up being my best friends this summer; Anna, Payton, and Molly. We learned about the brand, the history, and got a tour of all the buildings on campus.
Later that day during the happy hour, I met my line manager, Charlie Kirihara, who I immediately clicked with. He told me this summer I was going to work on an extensive intern project to design a female-focused flag football cleat and uniform kit with flag football being introduced at the 2028 LA Summer Olympics.
I haven't played flag football since I was 8 years old so I was excited to research where the sport has grown in the last decade or so. I was introduced to the team of designers at US Sports and was gifted a very lovely blue hackeysack, a family-size box of double-stuf Oreos, and a big welcome sign.
The first few weeks of the internship solely consisted of figuring out what was going on. There is an acronym or a term for everything at adidas. PU, TPU, BOA, rands, haptic, electric, impact, chaos, DCR, CR, CRO, CRI, SMS, DSG, CS1, CS2, in-line, pullover, and the list goes on and on. I tagged along to every meeting and wrote down everything anyone said and on the side, I was committed to learning about 1. the Flag Football space both in the US and globally and 2. where men's cleated footwear was failing our female athletes.
I learned that Flag Football is becoming an increasingly popular sport amongst high school female soccer, track, and lacrosse players. Many of these girls play multiple sports and use soccer cleats or sized-down men's American football cleats. The major issue with using men's cleats as a female is about fit. Women have a narrower stride, higher pressure on the lateral side, higher range of motion in the ankle, higher pronation, a flatter arch when running, and more. My research boiled down to men's cleats being too wide in the arch and heel, and lacking the proper arch support that women need.
I got to meet with the innovation team who are working on research regarding female athletes' gait, foot mobility and movement, and last construction. A last is a model of the foot that the research teams develop which acts as a base model for designers to create cleats. A high-quality/well-researched last can address many issues with fit and function. Nicole Schrier helped me understand what changes she is making on the new last construction and gave me a prototype of the last that her team was working on.
From there I needed to figure out what I wanted to accomplish in 12 weeks. I decided on designing a new tooling (outsole/cleat plate), new upper, sock liners, uniform jersey, uniform shorts, and sowing my own pair of sambas.
This was a lot of stuff.
To save everyone the trouble of reading my 60-day journal in full depth. I will give an overview of the process of each of these items with photos to make this 3-month extravaganza digestible.
I decided to explore this peacock story that came from my understanding of aggression tactics in American sports. Peacocking is "a way to flaunt one’s physical attributes while at the same time baiting an opponent. And it is this baiting element that ultimately sets this form of aggression apart from actual fighting. For the ultimate goal is not to injure, but to provoke. Whereas in a real fight, one might lead with their fists, or maintain a potential striking or protective distance, the combatants in these examples immediately enter an “intensely personal, intimate zone"
Flag football is a non-contact sport which means players must use tactics other than physical aggression to dominate other players. From my interviews of female athletes in flag football, volleyball, and lacrosse I learned that girls love to be loud, showy, and self-expressive when it comes to footwear since uniforms in these sports are typically standardized and solid team colors. Shoes are what sets them apart on the field. "It's how scouts, family, friends, and fans can find me on the field," a Lake Oswego HS lacrosse player said to me.
Regarding the upper design process:
I wanted this cleat to be different. I wanted it to be loud, lightweight, and feminine. I began sketching this sock-like silhouette that featured a low-cut fast profile and heel cut out to lock your foot into the shoe externally. I knew that girls actually prefer the perceived support of a mid to high-cut cleat and added a full booty with a mid-cut topline. This way they wouldn't have to compromise on the look of speed and the comfort of a mid-cut.
From here I had my first DCR (Design Concept Review) where I presented my general direction to the design team for feedback. Feedback from this team rocks. It is constructive, and understanding. They always pushed me to explore more and more abstract concepts since I was creating a brand-new product.

I went back and forth between ideation and feedback before beginning my prototyping phase. The first step was to learn how a shoe gets put together. With the help of Harold A. and Mitch B., I learned about shell patterns and how to do physical drawings on a tape-up of a last. I went back and forth printing, taping, drawing, un-taping, and scanning until I got to the first stage of the shell pattern to submit for a pullover.
I met with Alois H., a literal development wizard, who helped me throughout the prototyping process to work with PCT (Product Creation Team) on creating samples of this cleat.

After receiving the pull over I went through many rounds of feedback and redlines to continue to dial the upper construction.
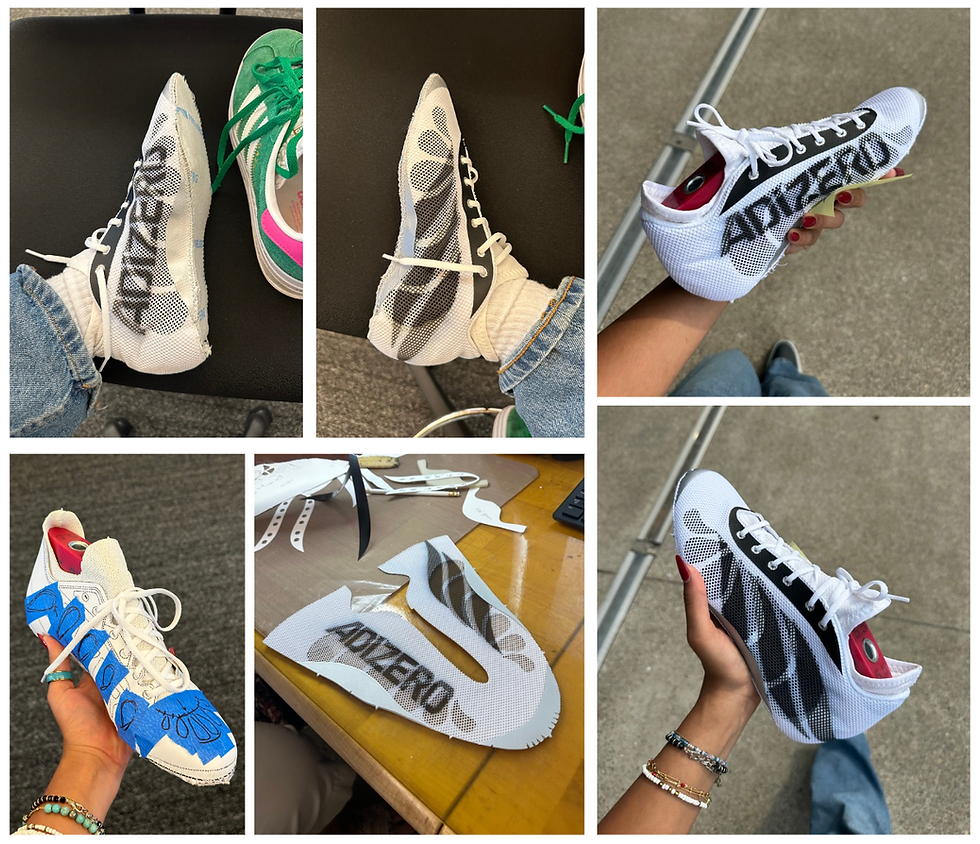
I wanted to focus on transparency and show the technology rather than tell the athlete it's there. I created a material map from the materials at the maker lab and PCT library to explain the exploded view of this upper.

I shadowed the PCT team to learn all the steps to make the shoe. Laser cut, glue, place, heat press, stroebel, lace, and more. Being able to watch Chris, Ron, Michelle, Brenda, and Josephine's work helped me understand what changes I needed to make to the construction of the shoe.
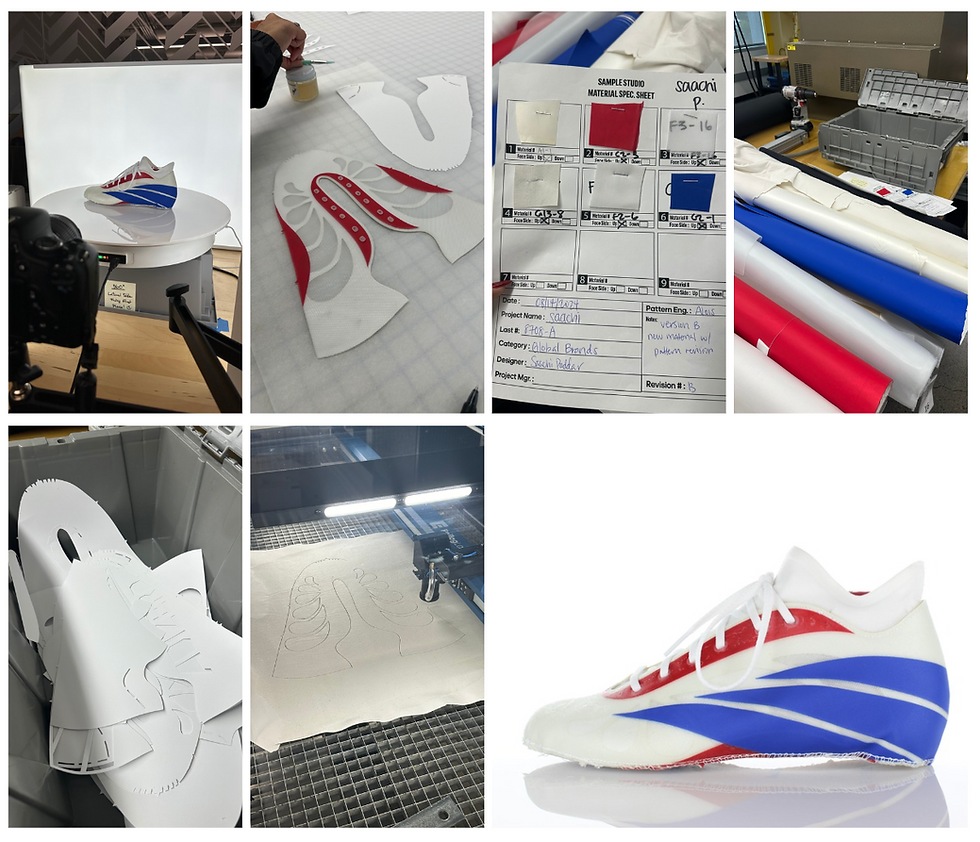
After this sample, it was time to put my CMG (Color, Materials, and Graphics) hat on. I love the CMG team at US Sports and got to shadow Charlie K., Maria I., Brett S., and Mike H.
I drew up tonal graphics for the medial of the cleat since it wouldn't feel like a product of mine if there wasn't something hand-drawn in it. I learned how to sublimate with Matty M. and Mike H. and created custom sock liners with hand-drawn graphics as well. Learning how to match an on-screen swatch to the in-person color proved to be a harder task than expected but after trial and error, I am really happy with how the sockliners turned out.
For CMG, I started with a mood board for the Peacock and Team USA colorways.

Charlie and Maria taught me how to create a CAD map and I created one for the Team USA and Peacock colorway. Charlie also gave me a smaller side project of creating CAD's regarding some on-field product that I can talk about at a later date!
After this, I finalized the redlines for the final sample and sat with PCT to shadow them while they made the sample. We ran into some material interaction issues where there was gapping between the eye stay and vamp :

However, I was able to problem-solve with the machines they had and get a final sample completed in a similar colorway as on-screen.
Regarding the tooling design process:
I began with the general silhouette of the adizero 13.0 tooling to understand how the form of a cleat plates looks. From there I sketched a rotational stud placement and structure using my research on female foot and cut movement.
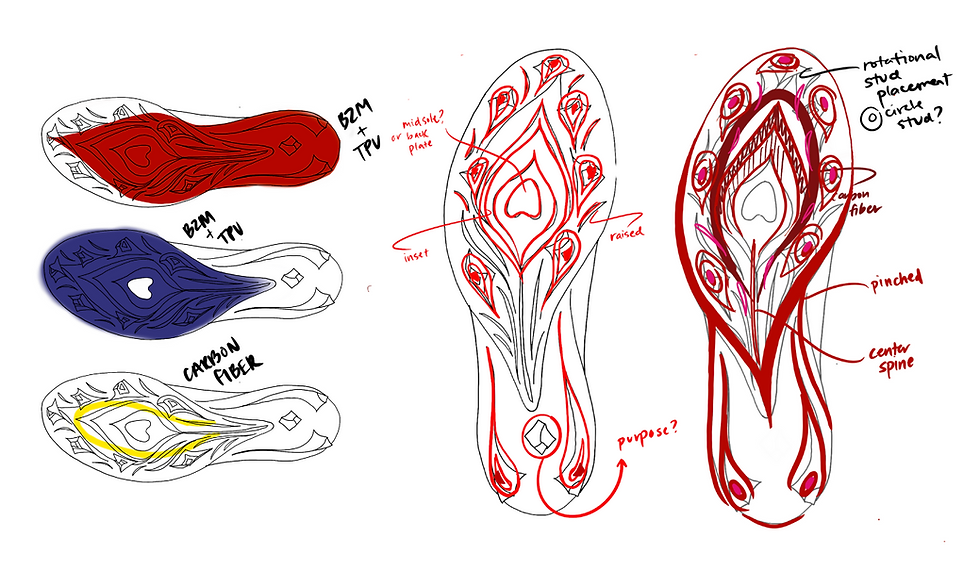
From here I needed to work on creating a 2-D techpack file that would explain the form of the tooling to a 3-D designer. I got the change to work with Nick Staub on this techpack where my Illustrator skills were absolutely put to the test. Thinking about an organic form in a 3-D space to create cross-sections was no joke.
After working on this file I met with Nick Martushev who helped me convert this blueprint into a 3-D file to be printed at PCT. We went back and forth with redlines to dial the final file.
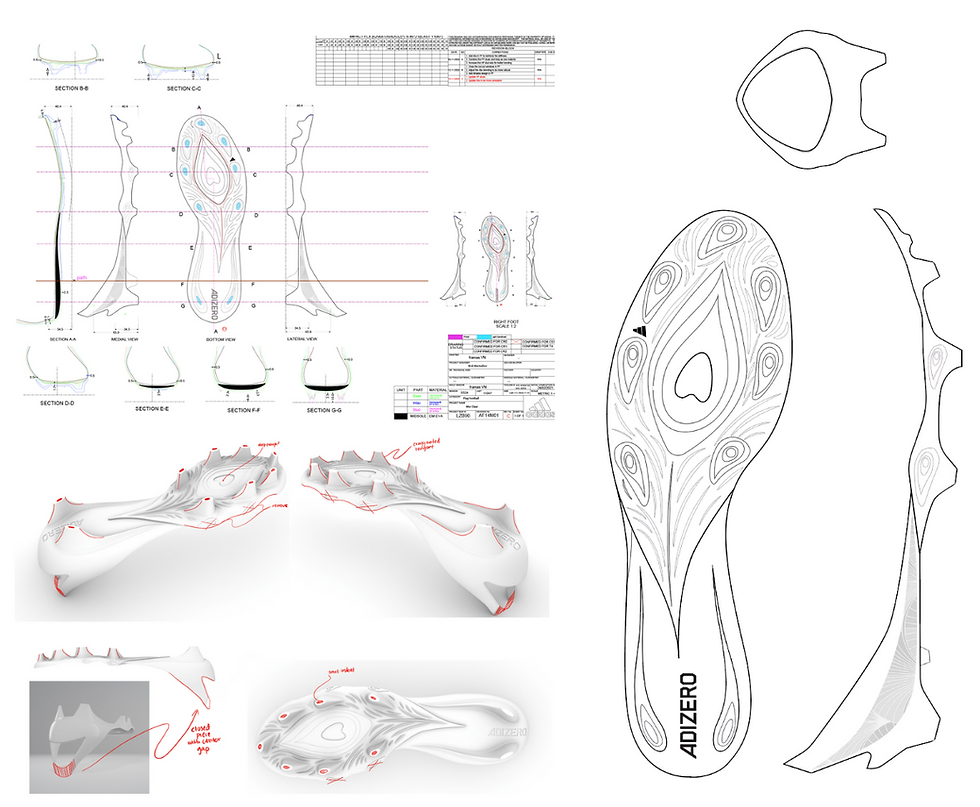
After this, I worked with PCT to get the 3-D file printed in a softer material that could be attached to the final sample of the upper. Michelle and Ron even went as far as to print a Nylon print of my tooling which can actually be wear-tested!
Regarding the apparel design process:

I began apparel with a branding exercise. I knew that I wanted to create a fitted jersey with fitted shorts but wanted to find a way to set this uniform apart from the catalog soccer jerseys most adidas highschool flag football teams currently wear.

I got the chance to attend multiple focus groups of flag players from all different levels of the sport and learn about what they liked and didn't like in their uniforms. Here are some of my findings in a shortened list:
No baggy uniforms
Roll shorts to be shorter and lower waistband
Easier to tuck jersey when jersey is fitted
Tiro 24 Soccer jersey fit but material is too thin
Mesh panels in sweat zones helps to cool down
Stretchy but not too stretchy
Need more flexibility in upper body (especially in arm space for QB and WR positions)
Shorts tore at the side seams frequently when grabbed
From here I created a fitted jersey silhouette with a matching pair of 3 inch inseam shorts. I removed the drawstring, pockets, and increased the strength of the seam construction by adding a double-felled seam.
I worked with Tanner S. to create a techpack of my idea in order to communicate with Stephan S. (also a development wizard) to have Apparel PCT complete samples for redlining. Stephan showed me his workflow in Clo3D and I worked on the resulting techpack.

While working through fit modifications with Stephan I explored the idea of creating a batwing shoulder body construction to increase mobility in the upper body and give the stripes a solid foundation to be attached to.
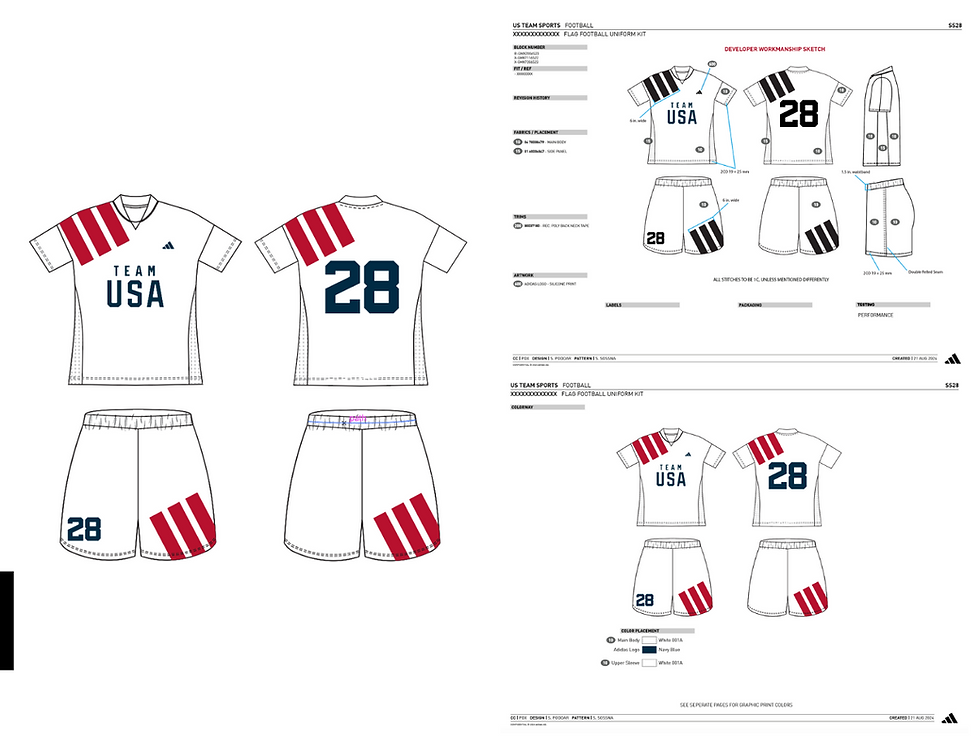
We submitted the pattern and tech pack file to PCT and in less than a few days I had a full uniform kit!
I sublimated the graphics for name and number to match the CMG on the tech pack file and had a few wear tests to see what I liked and didn't like. I had the shorts remade to adjust the branding read and then put it on the mannequin for my final intern presentation!
For my final presentation, I got the chance to present my project/research to 40 people within Adidas. I presented to individuals from US Sports, PCT, Basketball, CCP, the Intern 2024 Cohort, and more. It was so rewarding seeing everything come together in the end and to be able to talk about my project while passing around my product to the group.
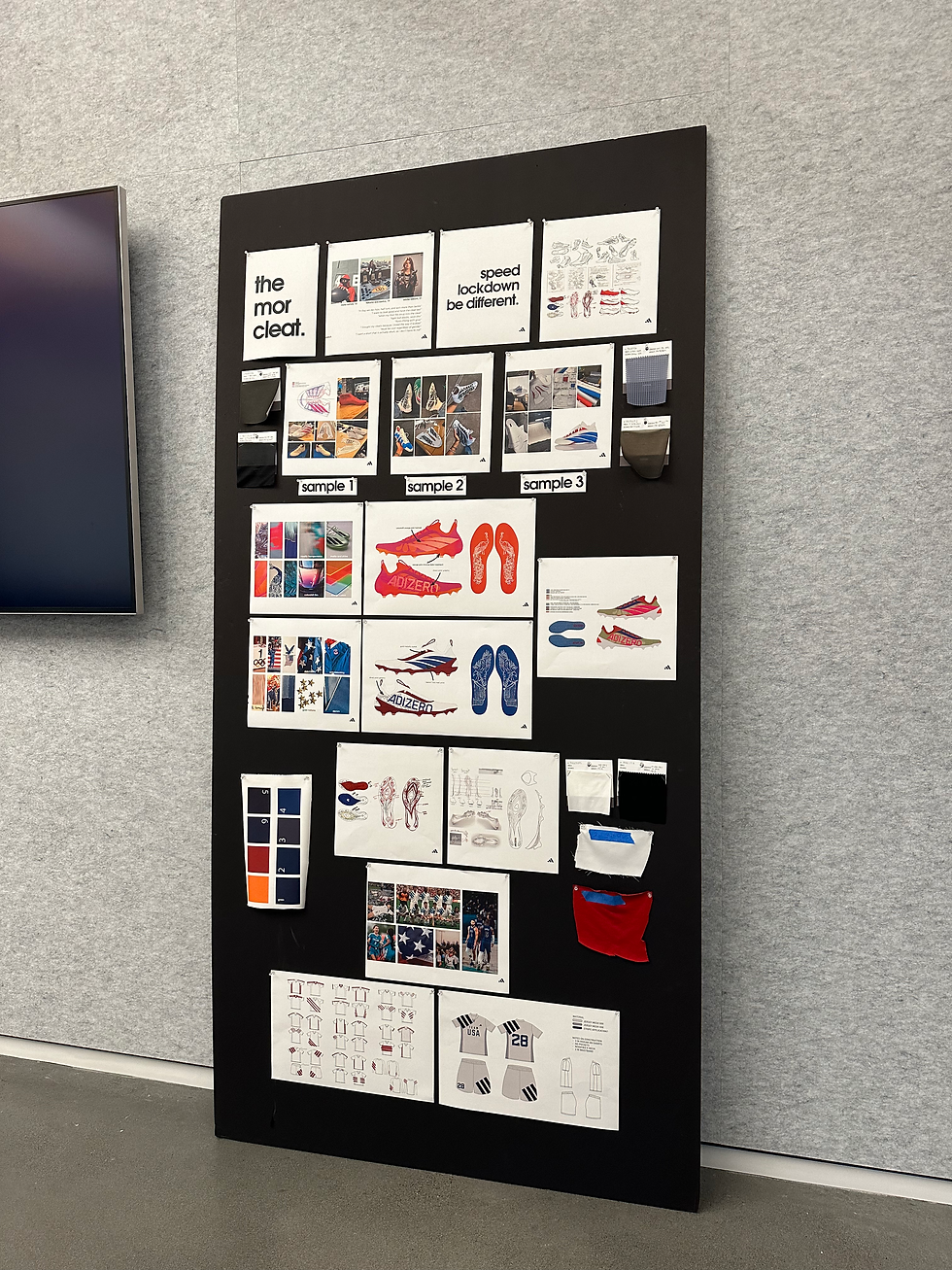
Later that day, I celebrated at a going-away happy hour with my team at a local spot near campus and said my goodbyes. I wrote little thank you cards for all who helped me, spent one final lunch with Payton, Molly, and Anna, and returned my laptop to IT, and that was it!
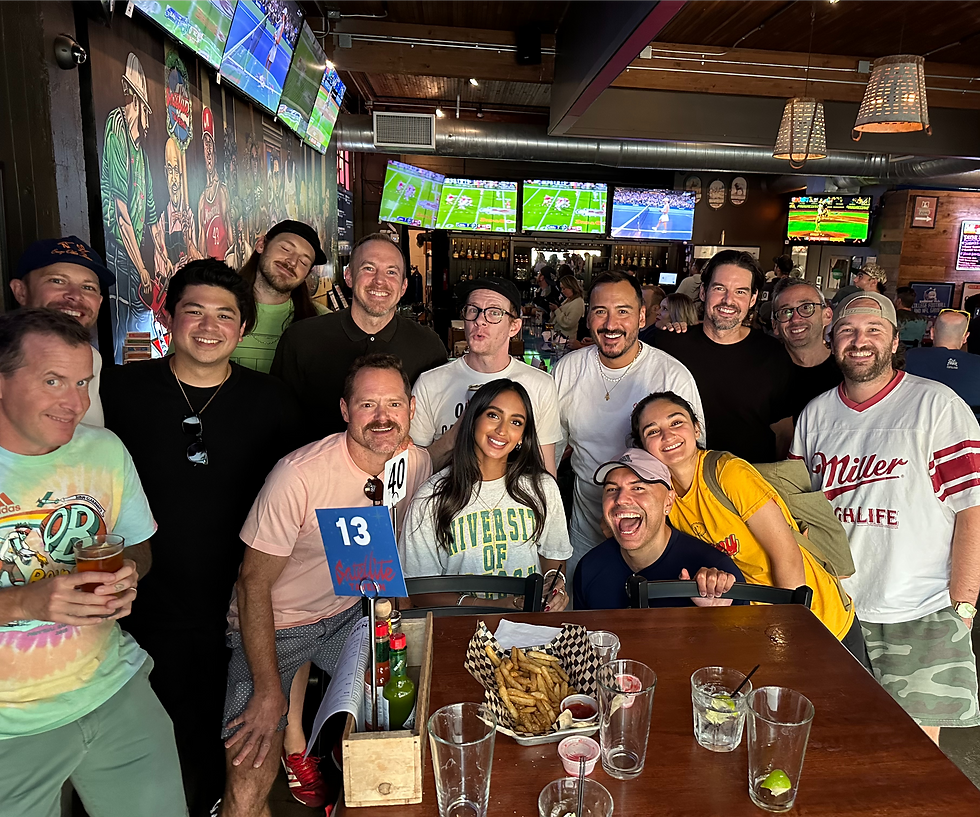
Some additional fun things I did as an intern this summer include: designing the Intern 2024 Jersey, cutting and sewing my own pair of sambas, running a half-marathon, attending the Adidas Creative Summit with Creative Leaders across Germany, LA, and Portland, participating in Intern Immersion Week, living on my own for the first time, and turning 21!!
I am so incredibly grateful to have met the people I've met at adidas this summer. US Sports is such a positive and collaborative family who have taught me much more than just design-related hard skills.
I know this was a long read but I thank you for reading all the way through!
I start my senior year in a week and I will be taking Tom Bonamici's Senior Footwear Studio. Super excited to be all moved into my first college house with the best roommates ever!!!
See you in the next blog post, I hope your summer was amazing.
Saachi Poddar
What an amazing experience, Saachi. Loved the process and details laid out. Reminded me of my first time in the SPM Lab at UO.